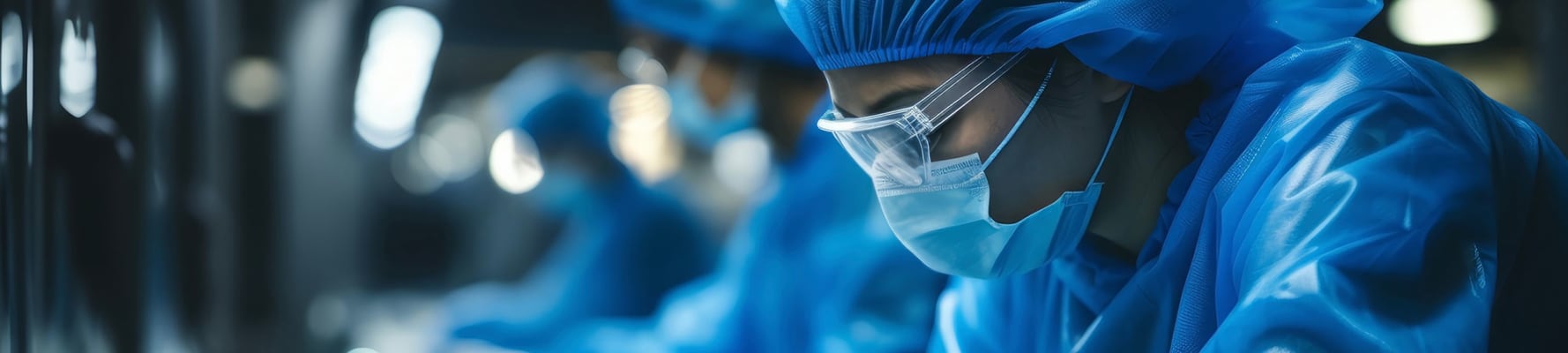
Industrie Pharmaceutique
Présentation générale du projet
Carrier vient d'installer trois groupes de production d'eau glacée centrifuges à eau AquaEdge® 19DV sur le site de production d'un grand fabricant pharmaceutique, dans le centre de l'Italie, en remplacement de ses trois groupes frigorifiques moins efficaces. Ces nouveaux groupes de production d'eau glacée vont refroidir les locaux de l'usine ainsi que les procédés industriels, et aider la société à atteindre ses objectifs de soutenabilité grâce à leur efficacité énergétique de haut niveau et au gaz frigorigène qu'ils utilisent, à l'impact réduit sur l'environnement.
Une pompe à chaleur AquaForce® 30XWHP doit par ailleurs être installée sur le même site pour récupérer l'énergie thermique dissipée par les procédés de production. Les groupes à eau glacée sont gérés par PlantCTRL™, le système intégré et innovant de Carrier, qui fait par ailleurs l'interface en toute transparence avec le BMS (Building Management System, Système de gestion centralisée du bâtiment).
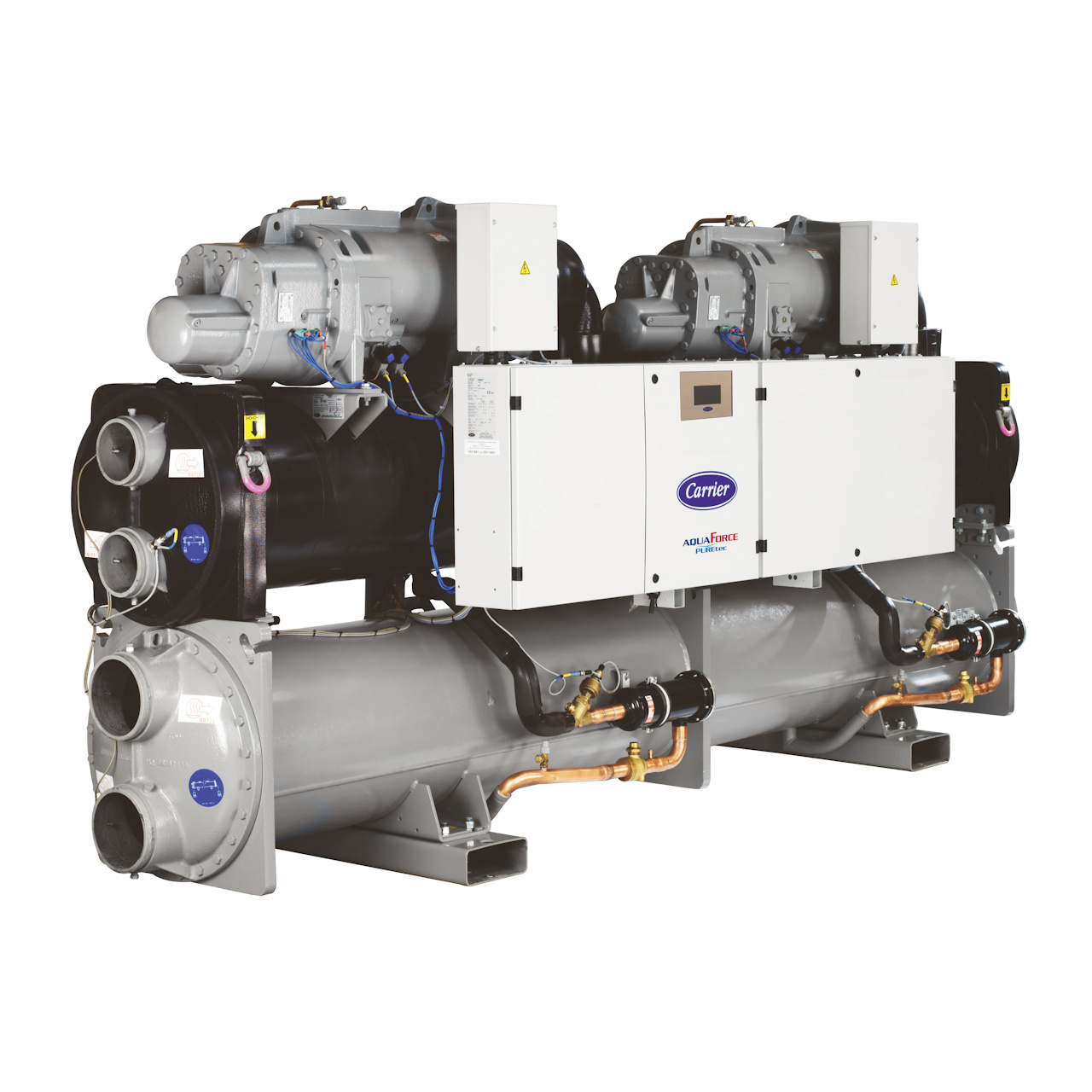
AquaForce® 30XWHP
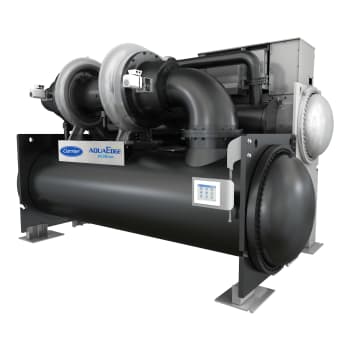
AquaEdge® 19DV
Les groupes de production d'eau glacée AquaEdge® de Carrier répondent à toutes les exigences en termes d'économies d'énergie, de confort acoustique, de viabilité du gaz frigorigène et de gains sur le coût total de possession, ce qui permet aux entreprises d'économiser l'énergie.
La solution
Le projet de remplacement des groupes frigorifiques sur le site de production d'un grand fabricant pharmaceutique à Lazio a été attribué à Carrier, pour l'excellence des performances qu'offre sa solution en termes d'efficacité énergétique, de fiabilité et de facilité d'emploi.
À la pointe de la technologie, les trois groupes de production d'eau glacée centrifuges AquaEdge® 19DV constituent une solution robuste et remplissant pleinement les objectifs de développement durable, en partie du fait qu'ils n'utilisent pas d'huile (leurs paliers en céramique se passent de graissage) et qu'ils mettent en œuvre un fluide frigorigène HFO respectueux de la couche d'ozone, le PUREtec™ R-1233zd(E), dont le potentiel de réchauffement global (PRG) n'est que de ~ 1. Autre particularité appréciable, ils sont capables de redémarrer rapidement, en 30 secondes (à l'aide d'une alimentation sans coupure) après rétablissement de l'alimentation électrique.
Par ailleurs, un refroidisseur/pompe à chaleur à vis et condensation par eau AquaForce® 30XWHP va être installé en mode “récupération totale” (ce qui sous-tend la production en même temps d'eau chaude et d'eau glacée) afin de récupérer l'énergie thermique produite à l'intérieur de l'usine, d'où des gains importants en termes de consommation d'énergie.
Les groupes de production d'eau glacée Carrier sont gérés par le système de contrôle PlantCTRL™ qui, en s'intégrant de manière transparente à la plateforme BMS déjà en place sur le site, permet de mettre en œuvre des stratégies pour gérer intelligemment l'ensemble de la production de froid et avoir une utilisation plus efficace de l'énergie et des refroidisseurs. Les algorithmes de diagnostic et de détection des défauts FDD (Fault Detection And Diagnostics) du système PlantCTRL™ sont un autre de ses avantages car, combinés aux services numériques de la plateforme Abound IoT, ils permettent à Carrier d'abaisser sensiblement les dépenses de maintenance par une détection préventive des pannes et des mauvaises conditions de fonctionnement (prognostics).
Grâce à l'installation de groupes à eau glacée Carrier et du système PlantCTRL™, il a été calculé que le fabricant pharmaceutique va pouvoir économiser jusqu'à 200 000 € par an sur ses coûts d'exploitation par rapport à la solution existante, avec un COP (coefficient de performance) moyen saisonnier calculé de 11,87 dans les conditions particulières du site.
Le client a eu par ailleurs l'opportunité d'assister à l'essai de réception FAT (Factory Acceptance Test) sur notre site de fabrication de Montluel (France). Cet essai de performance en usine est un processus au cours duquel nos produits sont évalués en termes de performances et de précision de fabrication, dans le respect du cahier des charges. C'est la garantie pour l'utilisateur final que nos produits sont conformes aux exigences les plus strictes et qu'ils répondent pleinement aux objectifs dans l'enveloppe budgétaire fixée.