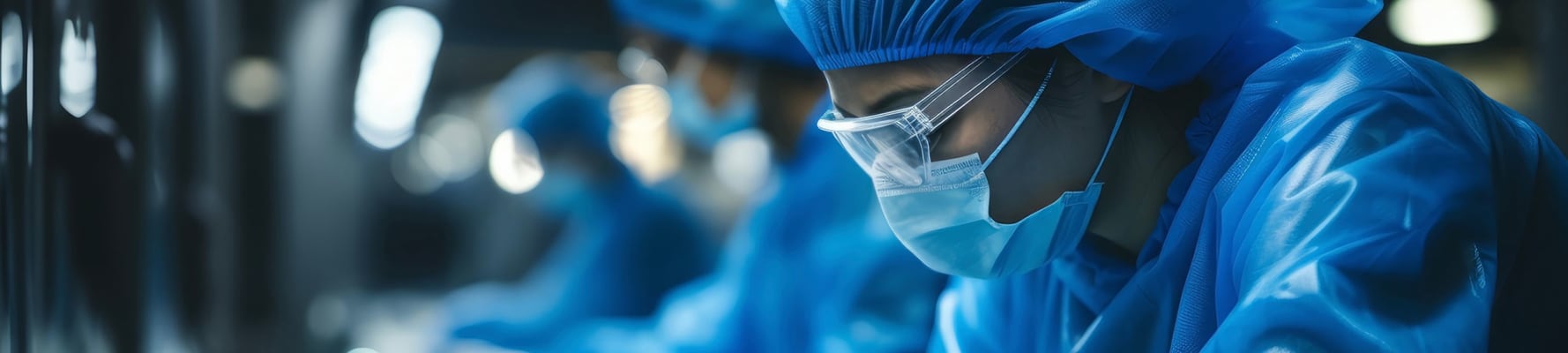
Pharmaceutical Industry
Project overview
Carrier has installed three AquaEdge® 19DV water-cooled centrifugal chillers at the production plant of a major pharmaceutical company in central Italy, replacing its three less efficient refrigeration units. These new chillers cool the factory building and plant processes, and help the company achieve its sustainability goals thanks to the units' high energy efficiency and the low impact of the environmentally friendly refrigerant gas used.
An AquaForce® 30XWHP heat pump is also to be installed in the same plant to recover the thermal energy dissipated in the production processes. Carrier's innovative integrated system, PlantCTRL™, controls the chillers and seamlessly interfaces with the existing Building Management System (BMS).
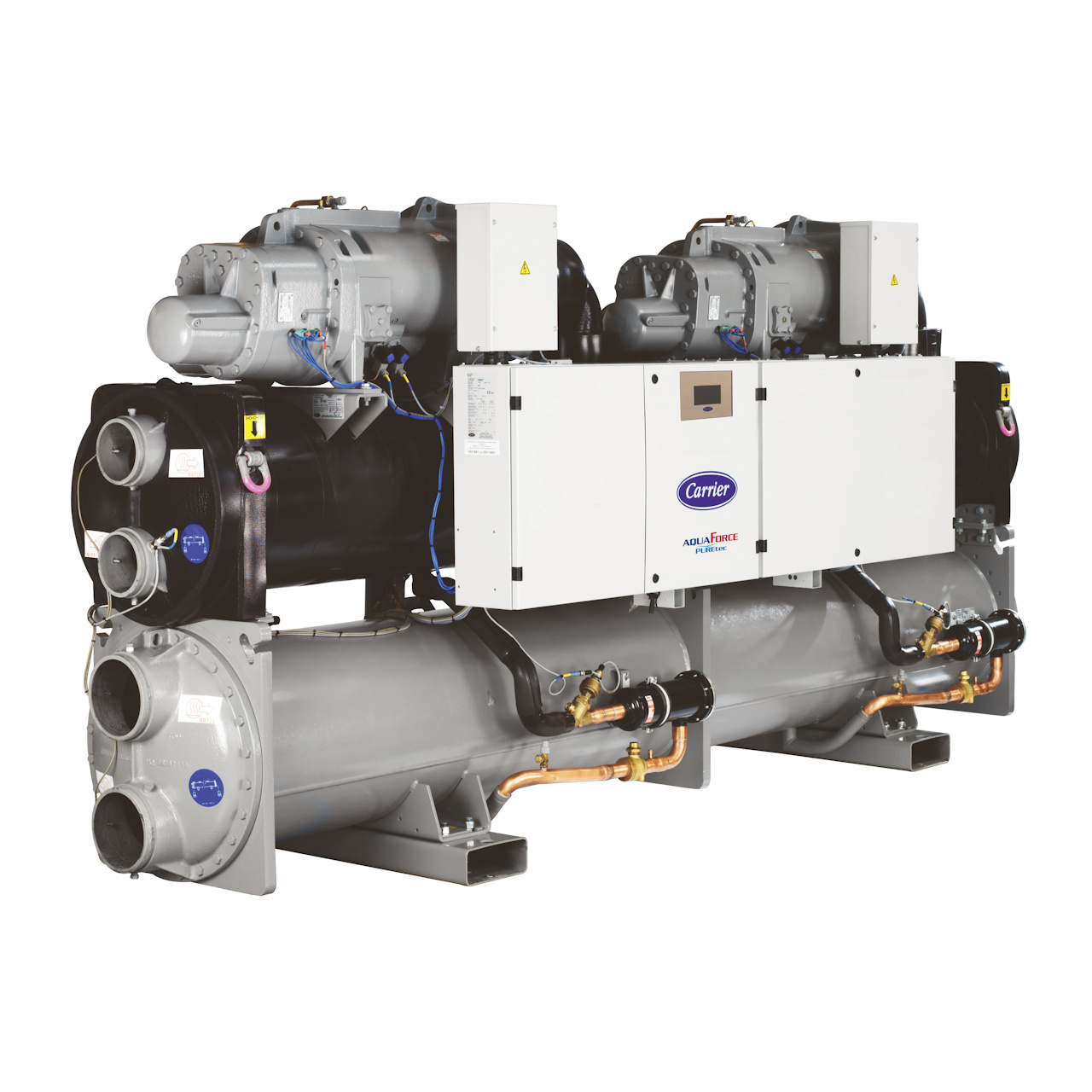
AquaForce® 30XWHP
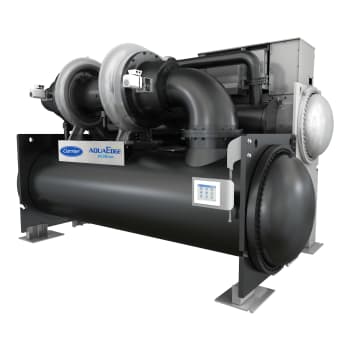
AquaEdge® 19DV
Carriers' AquaEdge® chillers meet all requirements in terms of energy savings, acoustic comfort, sustainability of refrigerant gas and low Total Cost of Ownership (TCO), enabling companies to save energy.
The solution
The project to replace the refrigeration units in the production plant of a leading pharmaceutical company in Lazio was awarded to Carrier as our solution offers excellent performance in terms of energy efficiency, reliability and ease of use.
The three state-of-the-art AquaEdge® 19DV centrifugal chillers are a robust and highly sustainable solution, thanks in part to the fact they are oilfree (no ceramic bearing lubrication) and use innovative, ozone-friendly refrigerant HFO PUREtec™ R-1233zd(E), with a Global Warming Potential (GWP) of ~ 1. Another appreciated feature is their ability to restart quickly in 30 seconds (using UPS) after the power supply is restored.
Another AquaForce® 30XWHP water-cooled screw chiller & heat pump will be installed in “full recovery” mode (i.e. producing both hot and chilled water at the same time) to ensure the recovery of the thermal energy produced in the plant, offering great benefits in terms of energy consumption.
Carrier's chillers are managed by the PlantCTRL™ control system which, by seamlessly integrating with the BMS platform already in use at the plant, enables advanced strategies to be implemented for smart management of all refrigeration equipment and more efficient use of energy and of the chillers. Another benefit of the PlantCTRL™ system is its Fault Detection And Diagnostics (FDD) algorithms which, combined with the digital services of the Abound IoT platform, enable Carrier to perform preventive detection of faults and incorrect operating conditions (prognostics) which significantly reduces maintenance costs.
Thanks to the installation of Carrier chillers and the PlantCTRL™ system, it has been calculated that the pharmaceutical company will be able to save up to €200,000 in its annual operating costs compared to the existing solution, with an average seasonal Coefficient of Performance (COP) calculated under site conditions of 11.87.
The customer also had the opportunity to attend the Factory Acceptance Test (FAT) at our production site in Montluel (France). Factory performance testing is a process in which our products are evaluated in terms of performance and construction accuracy, as determined by the design specifications. This guarantees the end-user that our products comply with the most stringent requirements, fully meeting the objectives, on budget.