Industrial Process Cooling: Big Cooling with Small Carbon Footprint
UK -
Innovations in cooling technology have revolutionised the way industrial processes are cooled. Stuart Peers, National Account Manager and Industry Vertical Specialist at Carrier Commercial HVAC UK & Ireland reveals how these advancements help to cut costs, improve the industrial process and reduce environmental impact for users.
The role of industrial cooling
Cooling is essential for various reasons within an industrial setting. Maintaining specific temperature conditions is crucial for product quality and operational efficiency. Perhaps the most valuable benefit of industrial cooling is to keep the production wheels turning and minimise the risk of equipment malfunctions or failures which cause downtime.
The transition from tradition to innovation
The journey from traditional cooling methods to modern innovations has been pivotal. Traditional methods relied on less sophisticated techniques compared to the innovations available today.
Water-based cooling systems, for instance, used large quantities of water circulating through pipes or channels to absorb heat from machinery or processes. The heated water was then redirected to cooling towers or other systems to dissipate the heat and lower the temperature before recirculation. Other methods, such as basic air ventilation and fans, were used to mitigate heat build-up. However, this method had limitations, especially in larger spaces or where precise temperature control was required.
Today’s industrial cooling consists of various equipment and systems designed to precisely manage temperatures. Depending on the specific need, equipment may include chillers, air-source heat pumps, air handling units, absorption chillers and drycoolers. These solutions have advanced significantly in recent times and feature cutting-edge technologies that meet the escalating demands of the modern industrial process.
Components such as compressors, fans and motors, heat exchangers and fan coils combine to operate at maximum efficiency to reduce energy consumption and improve reliability.
Advanced heat transfer mechanisms
Chillers work on the fundamental principles of thermodynamics and the refrigeration cycle. They transfer heat using a refrigerant that alternately absorbs and releases thermal energy through changes in pressure, temperature and phase (liquid to gas and vice versa).
Improving heat transfer mechanisms involve optimising the design of heat exchangers, coils and the refrigeration cycle. Increasing heat exchange surface areas, using more efficient refrigerants, enhancing compressor technologies and employing advanced control systems can help to maximise efficiency and performance.
These enhancements are evident in Carrier’s AquaForce® PUREtec™ 30KAVIZE air-cooled screw chiller. It is equipped with a variable-speed screw compressor and a reduced condensing surface and uses HFO R-1234ze refrigerant, which has a Global Warming Potential (GWP) of less than 1.
The 30KAVIZE meets the most demanding expectations in terms of energy efficiency and savings – both financial and space. The 30KAVIZE has a significantly smaller footprint compared to other models with the same capacity, approximately saving 3 metres in length.
Inside the unit, its technology can automatically adjust the cooling capacity based on the load variations of the industrial process.
The Carrier-designed third generation of “w” shape Novation® aluminium micro channel heat exchangers offer superior heat transfer performance and are approximately 10% more efficient than traditional coils, which has been confirmed through 2,000 hours of testing per CM1 (Carrier proprietary testing).
Furthermore, the 30KAVIZE operates at ambient temperatures of -20°C to 55°C and offers excellent energy efficiency. It has an average Seasonal Energy Efficiency Ratio (SEER) of 5,0 and a Seasonal Energy Performance Ratio (SEPR) of up to 3,7 (the ratio between annual cooling demand and annual energy input), which is 25% higher than EU Ecodesign requirements.
Harnessing nature for cooling
Taking advantage of naturally occurring lower outdoor temperatures is another way industrial cooling processes can become more efficient and cost-effective. When the outdoor air temperature is sufficiently lower than the required cooling temperature, for instance, during the winter or at night, it becomes an ideal source for cooling.
Carrier’s AquaSnap® 30RBP air-cooled scroll chiller, for example, can harness cooler outdoor temperatures thanks to its integrated free cooling.
In free cooling mode, the multiple scroll compressors stop, and only the fans are in operation. The unit’s smart controls switch to free cooling based on the needs of the application or climate conditions. Once the temperature exceeds the predefined threshold by 1K (Kelvin), free cooling kicks in and adjusts the air flow rate to optimise the chiller’s performance.
Thanks to free cooling, energy consumption is lower, and reliability increases due to reduced strain on mechanical components. This helps to extend the unit’s operational life, further boosting the return on investment and decreasing its carbon footprint.
Recovering wasted heat
In many industrial processes, there is room for improvement when it comes to utilising waste heat. In some industrial processes that run 24/7, an absorption chiller can capture waste heat such as steam or hot water and can recover and reuse it within the same process or other parts of the facility where it may be needed.
This heat recovery therefore improves the cooling process by lowering the need for additional energy input which further enhances the overall energy efficiency, reduces operational costs and minimises the impact on the environment.
The transition to ultra-low GWP refrigerants
Older cooling systems may have used refrigerants with high Global Warming Potential (GWP) and ozone-depleting properties, which required high energy consumption.
With the introduction of F-gas regulations in 2020, which phases down and phases out certain refrigerants with high GWP, Carrier responded responsibly and manufactured its own screw chillers that operate on HFO (hydrofluoroolefin) R-1234ze refrigerant.
This refrigerant has an ultra-low GWP below 1, has zero ozone depletion potential (OPD), and is not impacted by the F-Gas regulations.
Inside the 30KAVIZE, for example, the R-1234ze refrigerant has a 40% reduction in refrigerant charge thanks to its Novation micro-channel heat exchangers, offering energy efficiency gains of up to 5% when compared with units using R-134A.
Ammonia is a commonly used refrigerant in industrial cooling processes. Although this natural gas has a GWP of 0, precautions need to be taken due to its toxicity. If the refrigerant has a fault or leak, it can be extremely hazardous to employees, and the facility may need to be evacuated, causing significant downtime to operations. Hence why HFO refrigerants are a more attractive option and more cost-effective.
Smart controls for an intelligent cooling system
Another benefit of a modern cooling system is smart controls. Being able to precisely control temperature at any given moment can be critical in certain industrial processes, such as food processing, pharmaceutical production or mechanical engineering.
Intelligent controls, such as Carrier’s SmartVu™ allow users (and service teams) to analyse real-time data, such as electric energy consumption, cooling capacity and instantaneous and average seasonal energy efficiency ratios, so cooling can be delivered when and where it is needed in line with actual and forecasted demand.
Preventative and predictive maintenance to minimise downtime
Access to tangible data also allows for comprehensive service and maintenance. All the latest Carrier HVAC solutions come ready to connect to its suite of cloud-based services.
Abound™ HVAC Performance, provides actionable equipment portfolio insights to reduce operating cost, increase staff efficiency and improve uptime. This solution empowers the user to visualise, advise, and optimise the lifecycle and outcomes of the HVAC system.
Abound™ HVAC Performance helps improve productivity with real-time machine health notifications. Diagnostics and data are available to detect anomalies, rectify any issues quickly and minimise downtime. Service engineers can then provide preventative and predictive maintenance to ensure the equipment operates at the highest level throughout its lifecycle.
Plus, when the time comes, users can upgrade their systems via Carrier’s service and aftermarket team. This means users don’t have to always purchase brand new equipment to achieve higher equipment performance or energy reduction measures.
Upgrade to save
State-of-the-art HVAC technology with advanced heat exchangers, efficient refrigerants and smart controls has helped to improve the efficiency and effectiveness of industrial process cooling.
Many of these advancements are designed to support Green Building Design and are indispensable for modern industrial cooling processes because of their precise temperature control and substantial energy, cost and carbon savings.
As the industry continues to evolve, the adoption of innovative cooling technologies will help users stay competitive, achieve sustainability goals and optimise operational efficiency.
If you would like to upgrade or improve your cooling system, contact [email protected].
Author details
Stuart Peers has worked in the industrial HVAC industry for 20 years. He is the National Account Manager and Industry Vertical Specialist at Carrier Commercial HVAC UK & Ireland.
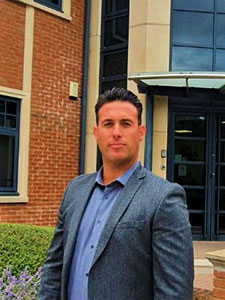
Stuart Peers, National Account Manager and Industry Vertical Specialist at Carrier Commercial HVAC UK & Ireland.
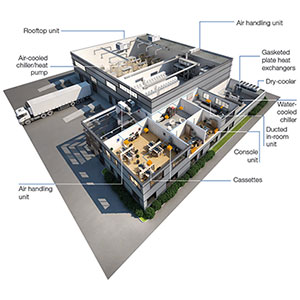
Some of the typical HVAC equipment used in industrial applications.
Carrier AquaForce® PUREtec™ 30KAVIZE air-cooled screw chiller.